The PHOENICE project developed a fully physical virtual test rig to support the calibration of the highly efficient spark ignition engine of the project.
Indeed, the availability of a reliable simulation platform is essential to effectively exploit the combination of the several features introduced to achieve the project target of 47% peak gross indicated efficiency, such as SwumbleTM in-cylinder charge motion, Miller cycle combined with high Compression Ratio (CR), lean mixture exploiting cooled low pressure Exhaust Gas Recirculation (EGR) and electrified turbocharging. Particular attention was paid to the definition of a combustion model capable of predicting engine burn rates in highly diluted conditions as well as the likelihood of abnormal combustion phenomena such as knock. A set of preliminary experimental measurements carried out on the first engine prototype was used to assess the reliability of the developed digital twin.
Afterwards, the 1D-CFD model was used to identify, under steady state conditions, the optimal setting of calibration parameters in terms of intake valves actuation, throughout the whole engine operating map. Findings demonstrated that the model achieved a satisfactory correlation with preliminary experimental measurements performed at ʎ = 1 and EGR rate = 0 lean reached the target of 47% peak gross indicated efficiency at part load. When operating at full load, the use of cooled low pressure EGR significantly reduced knock likelihood and permitted to avoid any mixture enrichment, allowing for the achievement of performance targets without incurring in fuel consumption penalties.
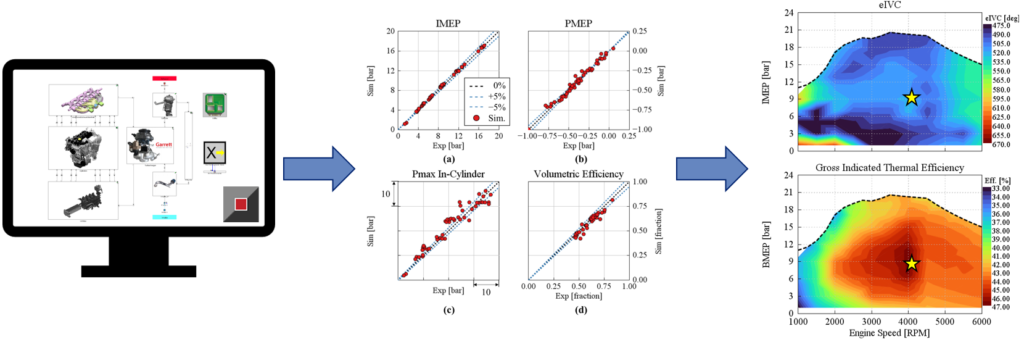